RRD Facility Spotlight: Kirk Road
2/3/2020 RRD
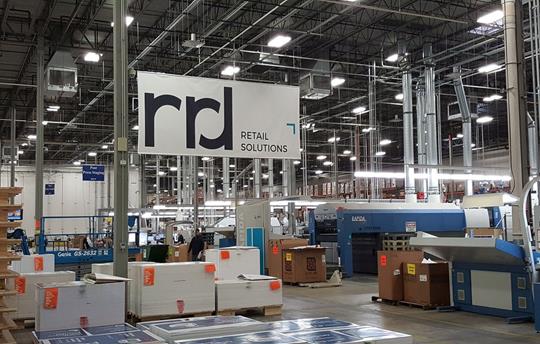
When it comes to our clients’ print-related needs, you might say RRD’s Kirk Road facility in St. Charles, Illinois, is everyone’s darling — and for good reason(s).
Commercial and large format printing? ?
State-of-the-art offset and digital printing? ?
Large scale kitting? ?
Distribution services? ?
All under one roof? ?
We recently touched base with Todd Arnett, the facility’s Director of Business Development, to learn more about the Kirk Road appeal and what’s making it stand out in the print crowd.
What about the Kirk Road facility makes it unique in the current marketplace?
Todd Arnett (TA): One word, vast. From capabilities to capacity, Kirk Road has everything available on a large scale — under one roof — so no matter the size of a request, we’re in a position to handle it.
There are a tremendous amount of services and solutions packed into this plant, including a wide variety of print technology, design work, finishing, kitting, pack out, and storage.
That’s something very few printers can lay claim to. Almost no other facility has warehousing and fulfillment in the same building as manufacturing.
It translates to our customers getting more consistency in their products, heightened speed-to-market and tighter turnaround times. Logistically speaking, everything is much more simple.
If you had to narrow it down to one, what do you consider Kirk Road’s forte?
TA: Complex kits. When it comes to complex kits at a large scale, no one else can handle what we do here — and I’ve been in the industry for a long time.
We use all of RRD’s proprietary software systems to the fullest extent, and run 24 hours a day, seven days a week. So when there's a project that requires thousands of kits containing several hundred different printed elements, there’s only one place that can do that: Kirk Road.
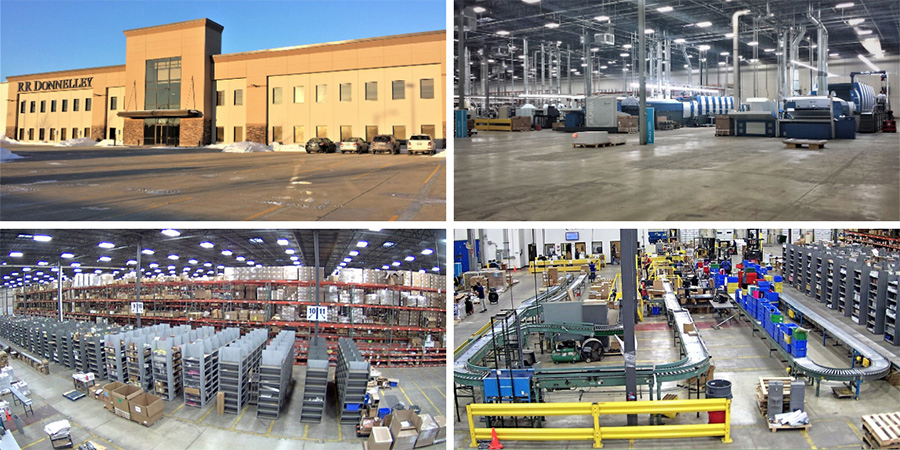
Can you share a recent success story that showcases this capability?
TA: Yes, and it involves a national home improvement retailer with over 3,500 stores. We provide them with monthly signage kits containing both generic and personalized items for each location.
We created an ordering portal that each of its locations could use to place orders for posters and end caps with store-specific product images, pricing, and details. This meant that every order could be tailored to the needs of the store — reducing waste and increasing engagement.
READ: Signage Localization — How it's reducing signage waste, accelerating speed-to-market, and empowering in-store staff
Each of the monthly sign kits included up to 150 different components and were shipped with a component list that detailed the items within, confirming their order. Besides simply including the information the store requested, each kit was automatically customized using variable data from each location. Depending on the order, we used different carton and tray sizes in each kit to minimize bulk and reduce freight prices, while still protecting the product during shipping.
In the end, we were able to take an online order from any one of the retailer’s 3,500 locations and deliver a final product to that store within 25 business days. This was an unprecedented level of speed and detail that other facilities simply can’t achieve.
When talking about Kirk Road to an RRD associate or potential client, what’s the one thing you find yourself repeating time and time again?
TA: You have to tour it. Whenever I walk through the facility with someone for the first time, they’re just blown away by the capacity. In the same building, they also get to see first-hand the work we’re doing — enormous, error-free print jobs.
Again, it’s highly unusual to have everything under one roof. It’s an eye-opening and reassuring experience, for sure. One that has also led to the start of new business relationships.
To learn more about this facility, visit our Kirk Road location page for capabilities and certifications.