Simplex Laser Printing Streamlines Parking Placard Production | Government
10/26/2020 RRD
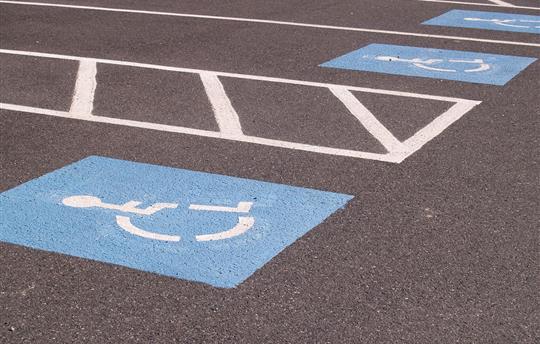
A simplified yet collaborative approach leads to an efficient solution for a state government agency
CHALLENGE
A southwestern state was using a cumbersome, multi-step process to produce handicap placards for designated residents. Inherent problems included:
- Three full-time employees (FTE) required to produce 300-400 placards daily
- Unreliable, inadequate heat seal machines that burned out regularly, costing several hundred dollars in repairs per incident
- Extreme hot weather, which periodically affected the placards’ physical integrity and legibility
- Weak consistency and accuracy in production and coordination
SOLUTION
The collaboration between RRD’s sales rep, application engineers, the client, and the manufacturing team produced a flawless new product — a single 8 1/2" x 14" sheet that was die-cut into a butterfly hangtag, allowing both sides to be imaged with a one-sided laser printer.
The printing process was vastly simplified, satisfied all the statutory requirements, and provided a convenient solution for the end-user. The label material was also tested to ensure it would not wilt in extreme heat.
RESULTS
The very first production run of these newly-fashioned handicap placards was a success. The solution yielded substantial cost savings for the client: three FTE positions were reduced to one person working about an hour and a half to complete an entire day’s worth of printing. This freed up and redeployed resources to more core-related needs. Additional wins included:
- Two variably printed pieces were simplified down to one form/label and one simplex print pass
- The incidence of errors was resolved with variable date data
- Heat seal equipment and associated maintenance costs were both eliminated