Medtech Leader Revamps Complex Global Packaging Processes | Life Sciences
3/6/2024 RRD
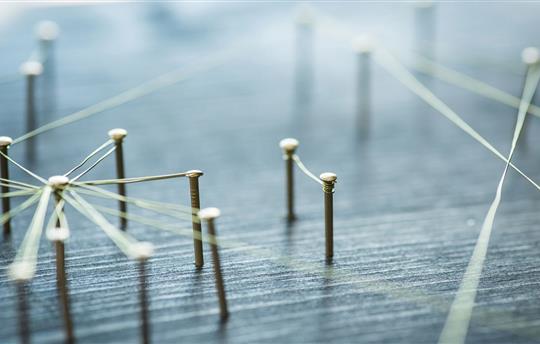
RRD’s comprehensive solution encompasses print management, supply chain optimization, and vendor auditing
CHALLENGE
One of the world’s leading medical technology companies operates 30 manufacturing sites throughout North America, Europe, and Asia, and has experienced years of continuous sales growth.
This unprecedented growth led to a series of intricate challenges in their packaging processes as they contended with hundreds of millions of units and thousands of direct packaging material SKUs. Stemming from acquisitions, the company’s diverse and outdated supplier base lacked a formal vendor onboarding and auditing process. This created complexities for direct packaging materials, and a number of challenges inevitably emerged:
- Inconsistent local supplier performance
- Labels and packaging procurement inefficiencies
- Fragmented quality assurance across regions, hindering standardization
- Direct packaging material stock replenishment issues
Ultimately, the company sought a trusted consultative partner to overhaul their print management processes, streamline their supply chain, and manage relationships with auxiliary suppliers.
SOLUTION
In response to these challenges, RRD engineered a comprehensive solution that positioned the company for sustainable growth. The proposed solution involved a thorough print management program and supply chain optimization strategy designed to consolidate suppliers, standardize processes, and streamline procurement through strategic management and forecasting.
RRD first took on the role of global supplier and printer for the company’s instructions for use (IFUs) booklets, folded carton and corrugated carton packaging, and labels — while also providing efficient material storage and rapid stock replenishment. RRD additionally took over the management of over 700 SKUs distributed to 11 international client manufacturing sites.
The following components comprised the multifaceted solution:
- A global account team was established to oversee sales and quality assurance, ensuring streamlined communication and exceptional service.
- Regional account teams were deployed to enhance customer service, production, and delivery order management.
- All RRD production sites adhered to Current Good Manufacturing Practices (cGMP) compliance, ensuring regulatory adherence.
- Ensuring consistent quality standards across all RRD sites became a key focus, facilitating product uniformity and reliability. Standardizing pre-press processes across facilities helped enhance productivity and output quality control.
- Proprietary demand forecasting tools and other supply chain management technology were deployed, optimizing materials usage and spend.
- Automation processes and user-friendly online tools were implemented to efficiently manage proprietary customer content, simplifying workflows.
- RRD standardized the vendor onboarding and auditing process, ensuring consistency and quality control for six external vendors. These vendors were onboarded and are managed as RRD vendors, freeing the company up to focus on core business practices.
RESULTS
Through this partnership with RRD, the company successfully transitioned from a fragmented regionalized supply base to a cohesive, strategic global supply chain. This move enabled the company to harmonize specifications, materials, and manufacturing across different regions, which resulted in the following benefits:
- Significantly reduced packaging spend: By optimizing their supply chain, automating forecasting, and achieving greater standardization, the company achieved substantial packaging process cost savings.
- Enhanced efficiency: Automation and streamlined processes improved efficiency, reducing lead times and minimizing disruptions.
- Improved quality assurance: Uniform quality standards across all RRD sites ensured the highest level of product quality and compliance.
- Global consistency: The global approach brought uniformity and consistency to the company's packaging materials and processes, promoting a seamless experience for both customers and end-users.
- Accelerated cycle times and faster speed to market due to deployed technologies.
Ultimately, the platform positioned the med tech company for continued growth. RRD's multifaceted solution demonstrated the team’s expertise, technological capabilities, and consultative approach to managing complex supply chain and print management challenges.