A Hybrid Approach to Building Supply Chain Resilience
11/4/2024 John Marrow
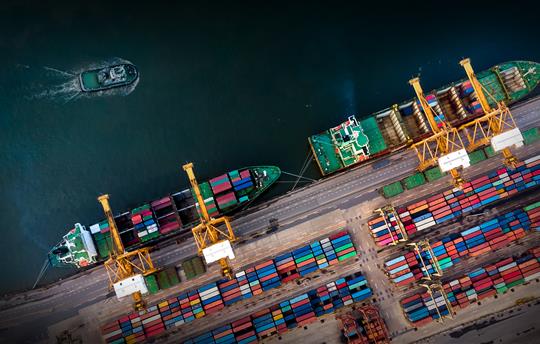
The COVID-19 pandemic underscored a significant weakness in offshoring models: their vulnerability to severe disruptions, potentially delaying operations for months.
While the pandemic was certainly a catalyst for rethinking offshoring strategies due to supply chain disruptions, other factors and events have also contributed to this shift. The below have spurred manufacturers to reconsider their supply chain options:
- The U.S.-China trade war: Tariffs on China, U.S. political pressure on companies to avoid manufacturing in China, and increasing labor costs throughout the country
- The United States-Mexico-Canada Agreement: The USMCA increased the content requirements for products to be labeled “made in North America,” providing manufacturers with an incentive to relocate their supply chains
- Militant raids on ships in the Red Sea: Attacks have caused cargo-carrying ships to change sea routes, resulting in longer voyages, increased transit time, and additional costs in fuel and crew pay
- The Russia-Ukraine war: The ongoing war in Ukraine has affected various material supply chains, including grain, fertilizer, and metals
Factors and events such as these have steered manufacturers toward other supply chain possibilities — including alternatives closer to home — for their supply chain options. In fact, 97% of supply chain decision-makers surveyed in RRD’s recent Future-Ready Supply Chain Report say they are planning at least some re-engineering of their supply chains in the next two years.
Reshoring and nearshoring options
As manufacturers and other companies look for offshoring alternatives, two options typically pursued are:
- Reshoring — relocating production from overseas sites back to the country where the manufacturer is headquartered
- Nearshoring — shifting the manufacturing to neighboring or nearby countries versus more distant, overseas locations
In fact, more than 60% of manufacturers have begun reshoring or nearshoring their production capacities, according to a Deloitte survey.
A manufacturer can often avoid the supply chain challenges noted above by utilizing a reshoring strategy and bringing production back to their home country. Reshoring can offer an abundance of additional benefits, including:
- Better lead times — decreasing the time it takes to produce and deliver a product to the final consumer
- Cost savings — by removing all customs and duty charges
- Greater control over production — while also allowing for more just-in-time manufacturing
- Local tax incentives — local and state governments will often offer companies fiscal incentives, including tax credits, rebates, and cash grants to relocate to a specific locality
- Ability to add “Made in the USA” and “Made in North America” labels
- Increased protection for intellectual property due to stricter regulations for IP rights in the U.S.
Nearshoring, the strategy of returning production closer to home, offers similar benefits. For U.S. companies choosing to relocate production or other tasks to Mexico, for example, benefits can include:
- Better lead times vs. overseas production due to proximity
- Increased speed to market vs. offshoring
- Cost savings — lower customs and duty charges vs. offshoring, plus cheaper labor costs vs. those in the U.S.
- Access to an additional talent and labor pool
- Greater control over production, allowing for more just-in-time manufacturing
- Ability to add “Made in North America” and other labels
- Added flexibility and agility — increased opportunity for in-person meetings, facility visits and evaluations, etc.
- Sustainability — provides a lower carbon footprint, aids company in achieving corporate environmental goals
- Favorable trade conditions
A hybrid alternative
An additional alternative — a hybrid model — provides the benefits of both nearshoring and reshoring. In such an approach, the manufacturer establishes operations or inventory (or both) in two or more locations. This supply chain tactic can serve to minimize risk in any single location.
For instance, a U.S. manufacturer with domestic production that is shipping products overseas for distribution in foreign markets could instead move production of overseas-bound products to a country or region closer to their final destination. This move would result in increased speed to market, improved sourcing capabilities for materials and supplies, and reduced costs overall. Meanwhile, for products aimed at domestic customers, the company could keep production and distribution in the U.S., freeing up resources for additional projects stateside.
Here's a real-world example of a successful hybrid model: A medical device company that designs, develops, and manufactures glucose monitoring systems ships products from Asia to facilities in the United States, Poland, and Singapore following production. At these facilities, they are then kitted and shipped to distribution centers, or they're held for direct shipment to company affiliates and retailers. This hybrid model results in lower component and finished goods inventories, improved product availability, and greater production flexibility.
Determining a strategy
While offshoring may have been the preferred course of action in the past, you’ll likely find that other options are more favorable to your organization in the current economic and supply chain climate.
Finding and joining forces with a partner with experience in all three options — offshoring, onshoring, and nearshoring — is critical when it comes to determining your supply chain strategy. By doing so, you’ll be able to avail yourself of that partner’s expertise in supply bottlenecks, process improvements, and best practices. Plus, you’ll be able to find the best solution for your organization to streamline your supply chain, boost productivity, and reduce costs.
Further disruptions to the global supply chain are always a possibility — whether those are a result of human events such as wars and bridge collapses, or natural causes like hurricanes and droughts. Accordingly, nearly half (48%) of supply chain leaders and managers report constantly updating their formal evaluation of supply chain risk, according to recent RRD research. By diligently evaluating all of your supply chain options, you can ensure that your company is prepared for whatever lies ahead.
John Marrow is the President of Supply Chain Solutions at RRD. To learn more about RRD's comprehensive supply chain solutions, visit rrd.com/supply-chain.